METHODS OF BOILER TESTING
When you choose JMI Mechanical, you’re getting skilled and friendly technicians with a trustworthy brand and reputation. We take pride in our work because we genuinely enjoy what we do, and it reflects in our service!
Unlocking Efficiency: Direct and Indirect Methods for Boiler Performance Assessment
In the realm of small industrial boilers, efficiency stands as a paramount metric for evaluating performance. This crucial aspect hinges not only on the boiler itself but also on the efficacy of its various components. At its core, boiler efficiency is a composite measure influenced by combustion efficiency, thermal efficiency, and several other contributing factors.
Combustion Efficiency: Maximizing Burner Performance
At the heart of boiler efficiency lies combustion efficiency, a metric gauging the burner’s adeptness at fuel consumption. This pivotal aspect is revealed through the examination of unburned fuel quantities and oxygen levels within the exhaust. Notably, combustion efficiency exhibits variations dependent on the type of fuel burned, with liquid and gaseous fuels typically yielding higher efficiencies compared to solid fuels.
Thermal Efficiency: Harnessing Heat Exchanger Effectiveness
Thermal efficiency stands as a hallmark of a boiler’s heat exchanger’s ability to effectively transfer heat energy. However, this efficiency can be hampered by scaling and soot formation on boiler tubes, impeding the optimal exchange of heat.
Direct Method Unveiled: Assessing Efficiency with Precision
The direct method of testing boiler efficiency, often dubbed the input-output method, offers a straightforward approach. It relies solely on comparing the output, typically steam, with the input, namely fuel, to gauge the boiler’s efficiency. This method is encapsulated in a simple yet powerful formula:
Boiler Efficiency = (Heat Output / Heat Input) x 100
Measurements Required for Direct Method Testing of Efficiency:
To execute the direct method effectively, precise measurements of both heat input and heat output are paramount. Here’s a breakdown of the key measurements needed:
Heat Input: The determination of boiler efficiency hinges on accurate measurements of both heat input and heat output. For heat input, the calorific value of the fuel and its flow rate, either in mass or volume, are crucial factors.
Solid Fuel: Measuring the flow rate of solid fuels like coal presents unique challenges. Typically, mass-based measurements require specialized apparatus installed within the boiler premises. Samples collected are securely sealed and dispatched to laboratories for meticulous testing.
Liquid Fuel: Assessing the flow rate of heavy fuel oil demands attention due to its viscosity, which fluctuates with temperature. While meters installed in combustion appliances provide approximate readings, it’s advisable to employ calibrated meters tailored to the specific fuel type.
Gaseous Fuel: The measurement of gaseous fuels necessitates correction for temperature and pressure variations. Gas meters, deployed for this purpose, require meticulous calibration for precise results.


Heat Output Measurement
Measuring the heat output of a boiler entails employing various methods tailored to its design and scale. For steam boilers, the installed steam meter is the go-to instrument for measuring the flow rate. Conversely, with smaller boilers, the feed water can be accurately gauged by calibrating the feed tank. It’s crucial to factor in the heat addition utilized for converting feed water into inlet steam when calculating heat output. Additionally, accounting for heat loss during continuous blowdown is essential to accurately assess steam heat.
Advantages of the Direct Method:
The direct method of testing boiler efficiency offers several distinct advantages:
1. Quick Evaluation: It enables a rapid assessment of efficiency, providing immediate insights into the boiler’s performance.
2. Minimal Factors: This method requires only a few key factors for calculation, streamlining the testing process.
3. Instrumentation: Compared to other testing methods, the direct method necessitates fewer instruments, simplifying testing logistics.
Disadvantages of the Direct Method:
Despite its efficiency, the direct method has some limitations:
1. Lack of Specificity: It fails to pinpoint the specific causes of low efficiency, offering limited insights into potential areas for improvement.
2. Limited Loss Calculation: The direct method does not comprehensively calculate various losses occurring at different stages of boiler operation, potentially masking critical inefficiencies.
3. Steam Quality Concerns: The presence of wet steam due to carryover can lead to incorrect evaporation ratio and efficiency calculations, undermining the accuracy of the results.
Indirect Method of Testing Boiler Efficiency:
The indirect method offers an alternative approach by measuring all losses occurring in the boiler. Efficiency is then calculated by subtracting these losses from 100. Unlike the direct method, minor measurement errors are less likely to impact the efficiency rate significantly in the indirect method. Various types of heat losses, including those due to hydrogen in fuel, dry fuel gas, moisture in fuel, carbon monoxide, air moisture, convection, surface radiation, and unburned losses in fly ash and bottom ash, are accounted for.
The formula for calculating boiler efficiency using the indirect method is:
100 – (Total Losses in the Boiler)
Measurements Required for Indirect Method Testing:
To measure boiler efficiency using the indirect method, the following parameters are essential:
1. Flue Gas Analysis: Parameters such as the percentage of carbon dioxide, oxygen, and carbon monoxide in the flue gas, along with flue gas temperature, are crucial.
2. Flowmeter Readings: Accurate measurements of feed water, condensate water, fuel, steam, and combustion air flow rates are indispensable.
3. Temperature Readings: Various temperatures must be monitored, including those of fuel, makeup water, steam, flue gas, combustion air, feed water, and condensate return.
4. Pressure Measurements: Pressure gauges are required to measure fuel, steam, draft, and combustion air pressures.
5. Water Conditions: Parameters such as Total Dissolved Solids (TDS), blowdown rate, and pH levels in the water must be assessed for a comprehensive analysis.

Advantages of the Indirect Method:
1. Comprehensive Analysis: The indirect method offers a thorough examination of boiler efficiency by achieving a complete balance between mass and energy for each individual stream, providing a holistic view of the system’s performance.
2. Identification of Improvement Opportunities: By accounting for various types of heat losses, the indirect method helps identify specific areas where efficiency can be enhanced, allowing for targeted improvement measures.
Disadvantages of the Indirect Method:
1. Time-Intensive: Conducting efficiency testing using the indirect method typically requires a significant amount of time due to the meticulous analysis involved, making it less conducive to quick assessments.
2. Laboratory Setting Requirement: The indirect method often necessitates laboratory settings for the analysis of various parameters, adding complexity and resource requirements to the testing process.
Factors That Enhance Boiler Efficiency:
1. Regular Maintenance: Proper maintenance practices, including cleaning, inspection, and tune-ups, play a crucial role in ensuring optimal boiler efficiency and performance over time.
2. Excess Air Control: Maintaining appropriate levels of excess air in combustion processes helps minimize energy losses and optimize fuel utilization, thereby enhancing boiler efficiency.
3. Fuel Quality: The quality of fuel used significantly impacts boiler efficiency, with clean and high-quality fuels typically yielding better results compared to lower-grade alternatives.
4. Boiler Insulation: Adequate insulation helps minimize heat loss from the boiler system, improving thermal efficiency and reducing energy consumption.
5. Water Treatment: Proper water treatment helps prevent scale formation and corrosion in boiler components, ensuring efficient heat transfer and prolonging equipment lifespan.
6. Optimal Steam Parameters: Maintaining optimal steam pressure and temperature levels ensures efficient steam generation and distribution throughout the system, maximizing overall efficiency.

Summary:
In conclusion, the evaluation of boiler efficiency through both direct and indirect methods is essential for ensuring optimal performance and energy utilization in industrial operations. While each method has its advantages and disadvantages, both provide valuable insights into the factors influencing boiler efficiency. At JMI Mechanical, we prioritize efficiency and reliability in all our boiler solutions, offering comprehensive maintenance services and innovative technologies to optimize performance and minimize energy consumption for our clients.
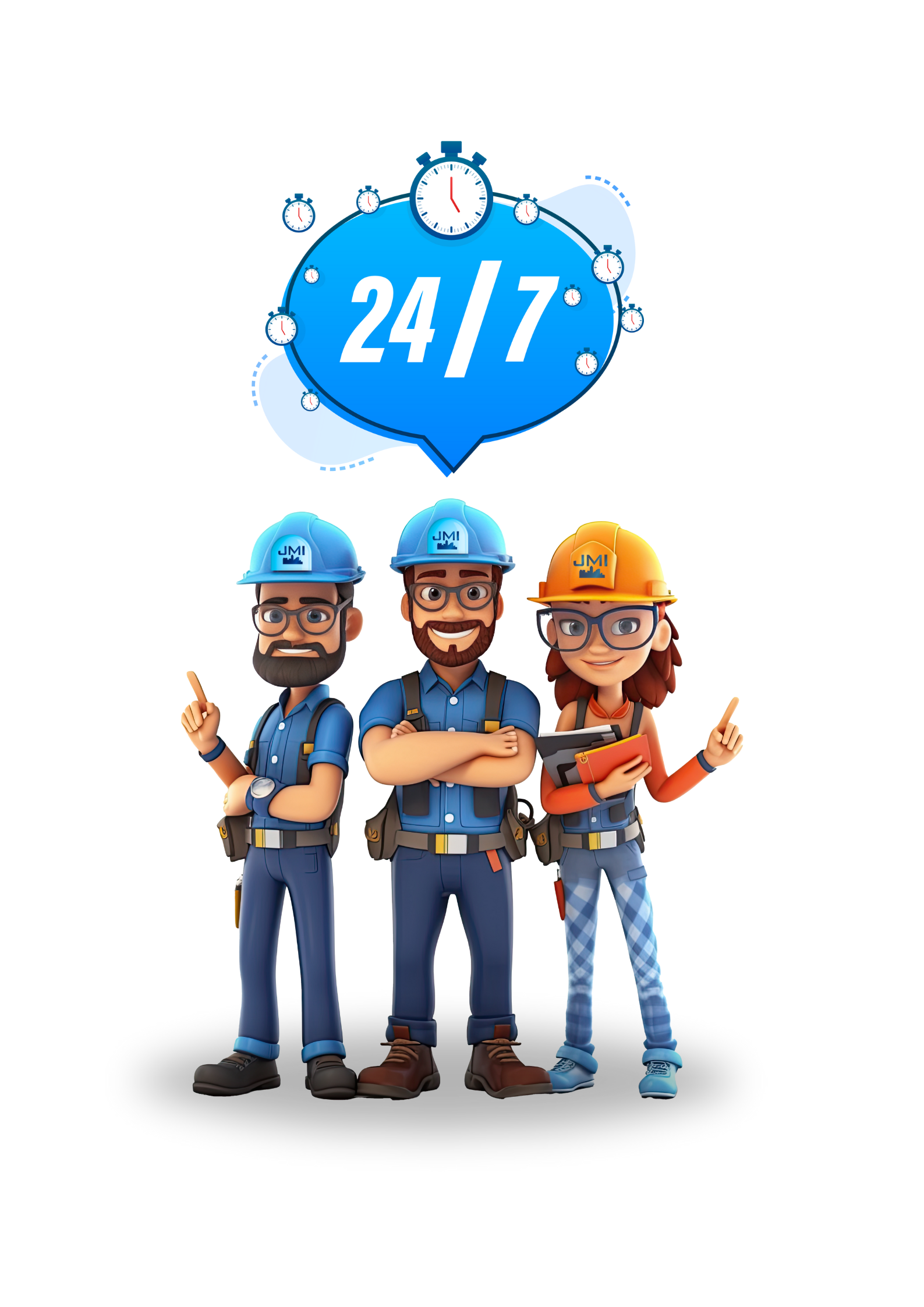
Reach Out To Us!
Do you have any questions or need advice? Feel free to reach out to us by giving us a call at 317-243-7180. We’re here to help and offer customized guidance based on your specific needs.
FREE QUOTE
Do you need help with HVAC or Plumbing service or maintenance? Fill out this form to get in touch with JMI Mechanical.
OFFICE LINE
1.800.555.6789
EMERGENCY
1.800.555.0000
WORKING HOURS
9:00am – 6:00pm
OFFICE LINE
1.800.555.6789
EMERGENCY
1.800.555.0000
WORKING HOURS