EDDY CURRENT TESTING
When you choose JMI Mechanical for Eddy Current Testing, you’re getting skilled and friendly technicians with a trustworthy brand and reputation. We take pride in our work because we genuinely enjoy what we do, and it reflects in our service!
“Exploring Eddy Current Testing: A Comprehensive Guide”
Eddy Current Testing
Eddy Current Testing (ECT) is a vital method used in Nondestructive Testing (NDT). It helps check objects made of conductive materials, like metals, for any hidden problems like cracks or defects. These issues could weaken the material or make it work poorly. The cool thing about ECT is that it doesn’t hurt the material while it checks it. Eddy Current Testing is like a superhero for metal stuff. It helps us make sure everything from airplanes to bridges stays strong and safe without having to break them apart to check. It’s pretty amazing how technology can help us keep things working smoothly!
Principle of Eddy Current Testing
Eddy Current Testing uses electromagnetic induction to check for defects in metal objects. Here’s how it works: When electricity flows through a coil, it creates a magnetic field that affects nearby metal. By passing electricity through a coil near a metal part, like a bolt, it generates a magnetic field that causes eddy currents to flow within the bolt. Changes in these eddy currents indicate issues, such as cracks or defects, in the bolt. By measuring these changes, we can identify problems. In simple terms, Eddy Current Testing uses electricity and magnetism to ensure the health and proper functioning of metal objects.
Equipment Used in Eddy Current Testing
Eddy Current Testing needs special tools to work right. It would help if you had things like probes or coils to make a magnetic field that switches back and forth. Then, these tools can find the eddy currents that come from that.
To control the test and look at the results, we use advanced Eddy Current Instruments. These gadgets help set up the test, handle the signals, and give us precise info about what’s going on. They’re like the brains behind the operation, making sure everything runs smoothly and we get the right answers.
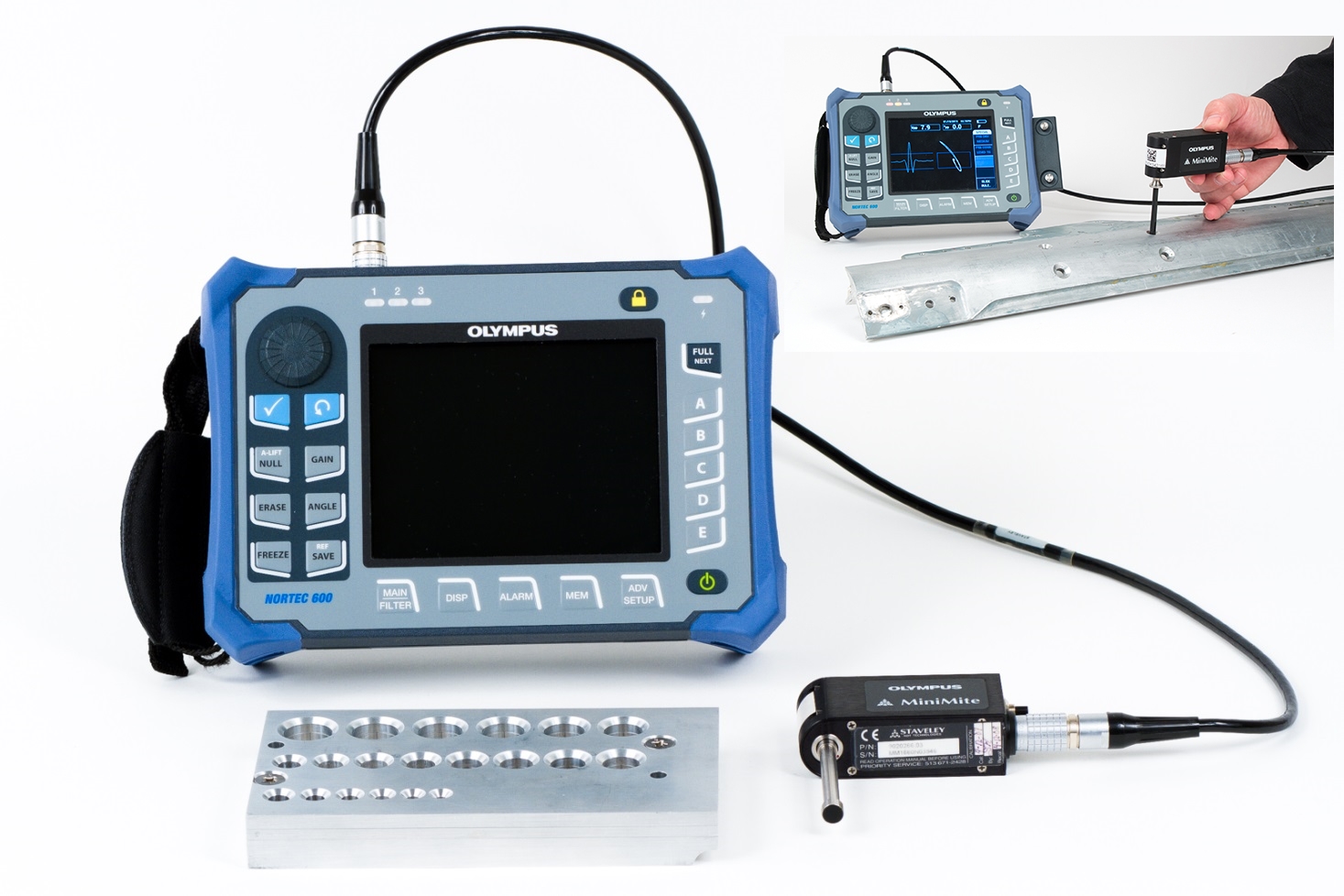
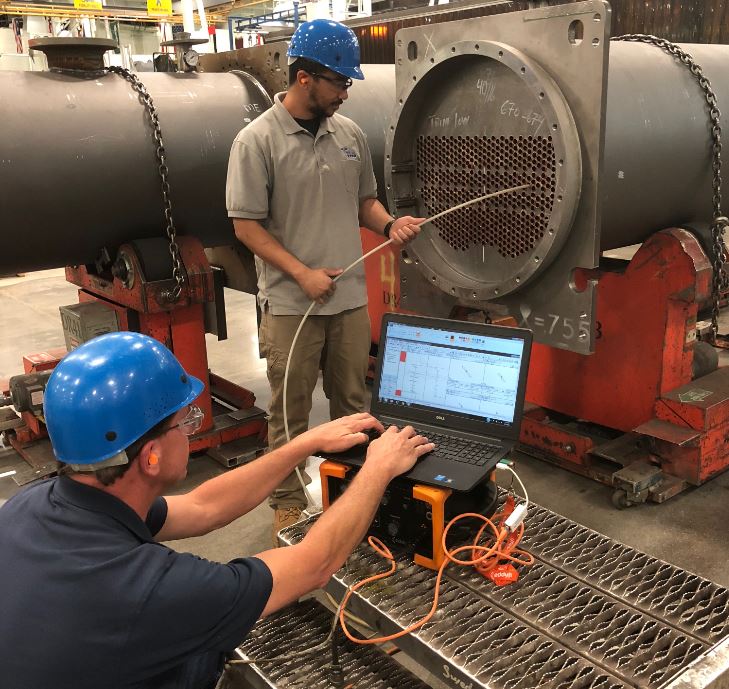
Applications of Eddy Current Testing
Eddy Current Testing is super useful in a bunch of different industries. In aerospace, it helps check airplane parts like engine blades and landing gear to make sure they’re okay. Car makers use it, too, to make sure important parts like crankshafts and suspension pieces are good quality. Even power plants use Eddy Current Testing to check if steam turbine blades and generator parts are still strong and working right. Overall, Eddy Current Testing is a super handy tool that helps keep things running smoothly in airplanes, cars, and power plants. It’s like a superhero that saves the day by finding and fixing problems before they get out of hand.
Advantages of Eddy Current Testing
Eddy Current Testing (ECT) offers a major benefit because it doesn’t harm the material being tested. Some testing methods can damage the material, but ECT is gentle and safe. Plus, it’s really good at finding tiny flaws that might not be visible to the naked eye.
When something needs to be inspected, like a metal pipe or a plane’s engine, we want to make sure it’s in good shape without causing any damage. That’s where ECT comes in handy. It uses a special technique that creates small electrical currents to detect imperfections in the material. And the best part? It doesn’t harm the material at all.
So, ECT is like a superhero for metal inspections. It saves the day by finding hidden flaws without causing any harm. That’s why it’s such a valuable tool in industries like aerospace, manufacturing, and engineering. It helps keep everything running smoothly and safely.
Limitations of Eddy Current Testing
Eddy Current Testing is a useful method for checking the surface of materials for flaws, like cracks or corrosion. However, it has its drawbacks, too. One of the main issues is that it can only find defects on the surface, not below it. So, if there’s a problem hidden inside the material, this test might miss it. Another thing to consider is how well the material conducts electricity. Suppose it’s very good at conducting electricity, like copper or aluminum. In that case, the test might not give accurate results because the electrical currents can behave differently in highly conductive materials.
Procedure for Conducting Eddy Current Testing
Eddy Current Testing is a method used to check the quality of materials, like metal, without causing any damage. The process goes through a few important steps to make sure the results are correct and trustworthy.
Each step is important to make sure we get the right information about the material we’re testing. It’s like taking a picture of something to see if it’s healthy or if there are any problems. This way, we can catch issues early and fix them before they become bigger problems.
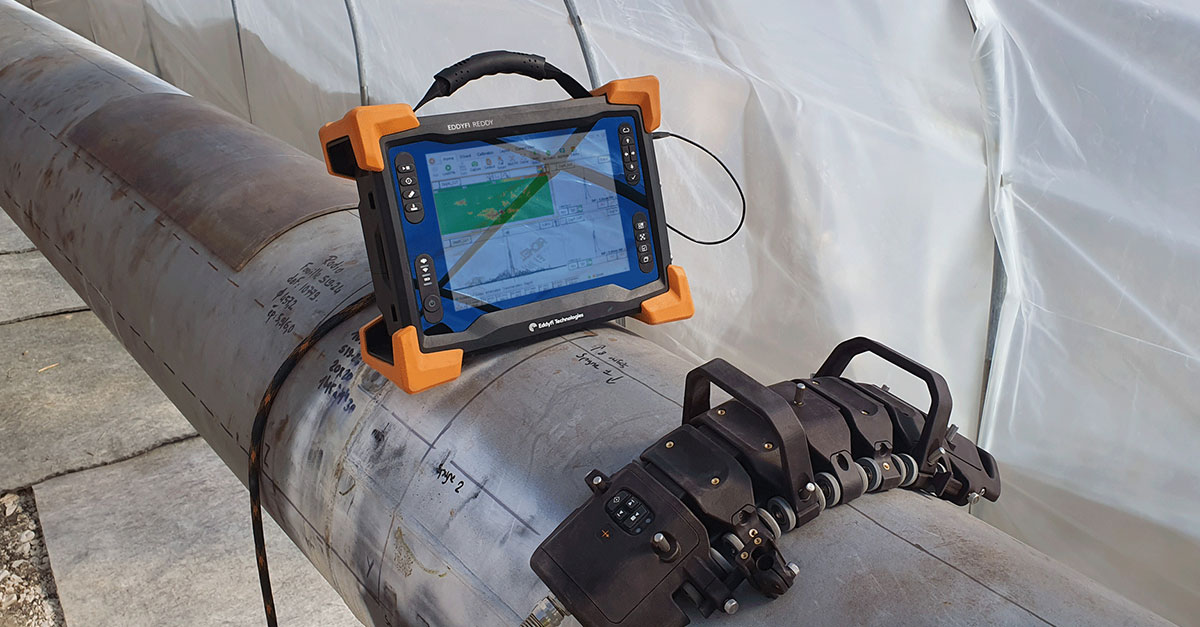
Interpretation of Eddy Current Testing Results
Interpreting the results of Eddy Current Testing requires expertise and a thorough understanding of the inspection technique. Skilled operators are trained to identify indications of defects, characterize their size and shape, and determine their significance in relation to the structural integrity of the component. Advanced signal processing techniques and visualization tools further aid in the interpretation process.
Comparison with Other NDT Techniques
While Eddy Current Testing offers numerous advantages, it’s essential to recognize its strengths and limitations in comparison to other NDT techniques. Magnetic Particle Testing, for instance, is well-suited for detecting surface and near-surface defects in ferromagnetic materials, whereas Ultrasonic Testing excels in evaluating the internal integrity of components through sound wave propagation.
Recent Advances in Eddy Current Testing
In recent years, significant advancements have been made in Eddy Current Testing technology, enhancing its capabilities and efficiency. Digital Signal Processing techniques have revolutionized signal analysis, enabling more accurate defect detection and characterization. Automated systems equipped with robotics and artificial intelligence algorithms have streamlined the inspection process, reducing human error and increasing productivity.
Training and Certification in Eddy Current Testing
Proficiency in Eddy Current Testing requires specialized training and certification to ensure competency and adherence to industry standards. Operators undergo rigorous training programs to familiarize themselves with equipment operation, inspection techniques, and data interpretation. Certification programs accredited by organizations such as the American Society for Nondestructive Testing (ASNT) validate the skills and qualifications of ECT practitioners.
Training and Certification in Eddy Current Testing
Proficiency in Eddy Current Testing requires specialized training and certification to ensure competency and adherence to industry standards. Operators undergo rigorous training programs to familiarize themselves with equipment operation, inspection techniques, and data interpretation. Certification programs accredited by organizations such as the American Society for Nondestructive Testing (ASNT) validate the skills and qualifications of ECT practitioners.
Cost Considerations in Eddy Current Testing
While the initial investment in Eddy Current Testing equipment and training may seem significant, it’s essential to consider the long-term cost-effectiveness of the technique. The ability to identify defects early on, prevent catastrophic failures, and prolong the service life of critical components ultimately translates into substantial cost savings and enhanced operational reliability.
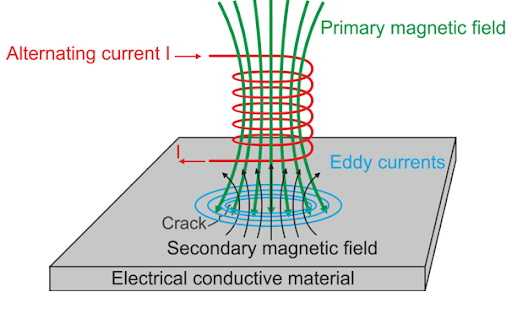
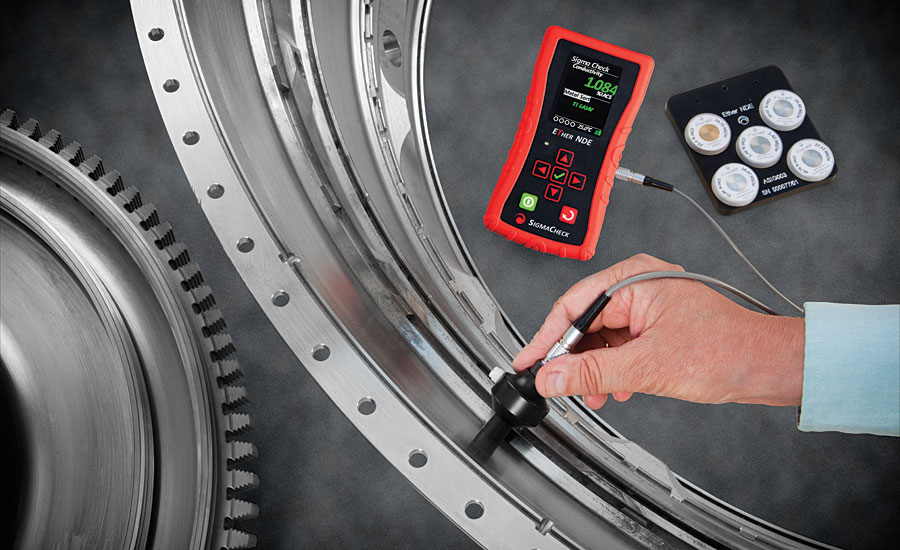
Case Studies and Success Stories
Real-world examples illustrate the efficacy of Eddy Current Testing in various industries and applications. From detecting fatigue cracks in aircraft fuselage to identifying corrosion in nuclear power plant piping, these case studies underscore the importance of proactive maintenance and quality assurance through NDT techniques.
Future Trends in Eddy Current Testing
Looking ahead, the future of Eddy Current Testing is poised for further innovation and integration with emerging technologies. With the advent of Industry 4.0 initiatives, there’s a growing emphasis on connectivity, data analytics, and predictive maintenance. Advanced sensors capable of real-time monitoring and continuous inspection hold the promise of revolutionizing asset management and enhancing safety across industries.
Ready to Schedule Your Eddy Current Inspection?
Are you ready to schedule your Eddy Current Inspection? Eddy Current Testing is a crucial method in Nondestructive Testing, providing excellent sensitivity, flexibility, and affordability. It’s used in various industries like aerospace, automotive, power generation, and petrochemicals.
Eddy Current Testing is like a superhero tool for finding flaws or defects without causing damage. It can detect tiny cracks, flaws, or changes in materials that could lead to big problems later on. Whether it’s checking airplane parts for safety or making sure pipes in a factory are strong, eddy current inspection gets the job done.
JMI Mechanical is here to help with all your eddy current inspection needs. We’re experts in this field and can assist customers anywhere in the world. Our team knows how to use eddy current testing to its fullest potential, ensuring accurate results every time.
If you’re ready to schedule your first or next eddy current inspection, don’t hesitate to reach out to us. Contact us today, and let’s make sure your equipment and materials are in top-notch condition.
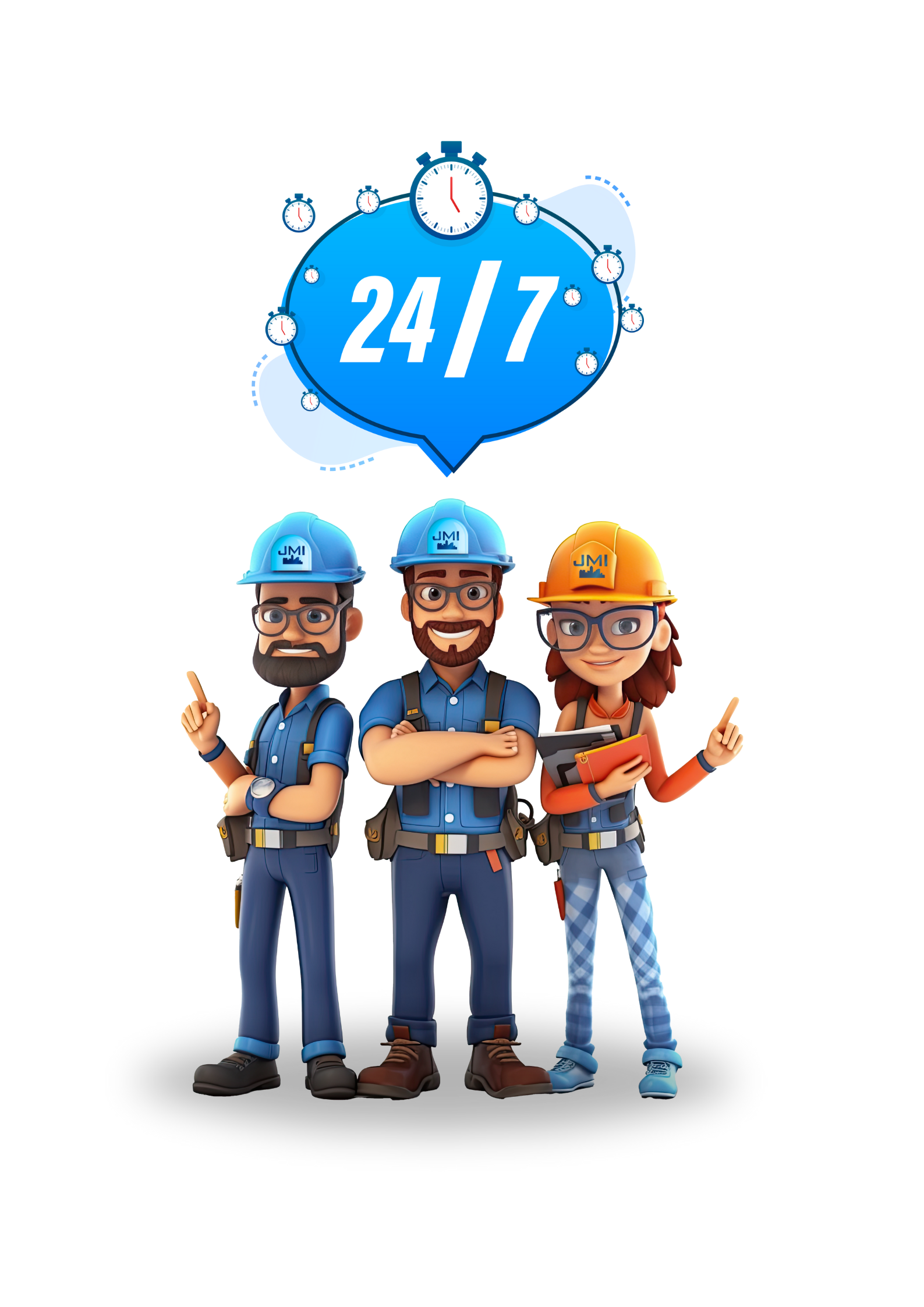
FREE QUOTE
Do you need help with HVAC or Plumbing service or maintenance? Fill out this form to get in touch with JMI Mechanical.
OFFICE LINE
ADDRESS
5610 Dividend Rd. Suite A, Indianapolis, IN 46241
WORKING HOURS
OPEN 24/7/365
OFFICE LINE
ADDRESS
5610 Dividend Rd Suite A, Indianapolis, IN 46241
WORKING HOURS