BOILER EFFICIENY TESTING
When choosing JMI Mechanical, you gain access to the proficiency of adept and friendly technicians from a well-known and reliable brand. Our dedication to Boiler Efficiency Testing is unmistakable in our operations, fueled by our sincere enthusiasm for our work, guaranteeing exceptional service on every occasion!
Discovering Boiler Efficiency: Testing and Understanding Performance
Boiler Efficiency Testing is crucial in today’s industrial landscape, especially regarding packaged firetube boiler technology. These boilers are indispensable for powering various processes and heating applications using steam and hot water. Their reputation for efficiency and cost-effectiveness makes them a preferred choice for energy generation across different sectors.
When evaluating boiler equipment, key factors like boiler type, maintenance requirements, and fuel consumption come into play. Among these factors, Boiler Efficiency Testing stands out as a critical measure. Essentially, Boiler Efficiency Testing quantifies the difference between energy input and output. Given that boilers typically consume a significant portion of the annual fuel budget, even minor improvements in efficiency can result in substantial savings. However, accurate assessment of efficiency demands reliable data based on proven performance to avoid misleading comparisons in fuel usage.
It’s important to note that the upfront cost of a boiler is just a fraction of the total investment. The majority of expenses arise from fuel and maintenance, underscoring the importance of making informed choices when selecting a boiler. Differences in design among boilers can lead to variations in efficiency performance, offering insights into anticipated operating costs.
While all boilers operate on fundamental thermodynamic principles, determining a maximum theoretical efficiency for a specific design sets a benchmark. Efficiency claims that exceed this theoretical value should be scrutinized, as they may not accurately reflect actual fuel usage.
Ultimately, the value of a boiler, the efficiency of its burner, and ongoing support throughout its lifespan contribute to overall efficiency. As industries strive for optimal performance and cost-effectiveness, prioritizing Boiler Efficiency Testing and understanding its implications remains crucial.
The Importance of Picking The Right Boiler
When considering an investment in a boiler, Boiler Efficiency Testing is crucial to prioritize the selection of a highly efficient model. Opting for a boiler with superior efficiency not only helps in saving on annual fuel costs but also ensures optimal utilization of your investment in the long run. Look for burners that have a proven track record of reliability in maintaining optimal air-to-fuel ratios over extended periods. The consistent efficiency offered by such models not only guarantees long-term savings but also provides a high level of reliability that is essential for uninterrupted operations. By focusing on these key aspects during the selection process, you can make a sound investment decision that will benefit you in the years to come.

To Replace or To Repair, That Is The Million Dollar Question
When it’s time to think about your boiler, you might wonder whether it’s better to fix the old one or get a new one. Here are some things to consider:
- Maintenance Costs
Think about how much you’ve been spending on fixing your old boiler. This includes emergency repairs, times when it’s been out of service, and the overall trouble it’s been giving you. These costs add up, even if they’re not always obvious.
- Boiler Performance
New boilers work a lot better than old ones. They have fancy features that help them run smoothly and efficiently. This means you’ll spend less on running them and have fewer problems in the long run.
Fuel Usage
Think about what kind of fuel your boiler uses. If it’s not very efficient or if you’re thinking about switching to a different kind of fuel, you might want to consider getting a new boiler instead. Even if upgrading your old one seems like a good idea, it might end up costing you more in the long run.
- Efficiency
How well does your old boiler work compared to a new one? A professional can help you figure this out by analyzing things like how much fuel you use and how your boiler room is set up. This can help you see if getting a new boiler would save you money on fuel and maintenance in the long run.
Efficiency Feature Comparisons
Are you aware of the critical role “Boiler Efficiency Testing” plays in distinguishing firetube boilers? Not all boilers are equal, and understanding the nuances can significantly impact overall efficiency.
It’s a common misconception that achieving optimal efficiency in firetube boilers is a complex endeavor. In reality, it’s about the deliberate incorporation of design elements within the boiler. Familiarizing yourself with these design distinctions can provide valuable insights into anticipated efficiency levels. Here are some essential design aspects to factor in when assessing boilers:
Number of Boiler Passes
The concept of boiler passes denotes how many times combustion gases traverse the heat exchanger. A higher number of passes translates to more opportunities for heat exchange. For instance, a 4-pass boiler maintains lower stack temperatures compared to a 2- or 3-pass configuration, resulting in enhanced efficiency and reduced fuel expenditures. This design enhancement also elevates heat-transfer coefficients.
Burner/Boiler Compatibility
The term “packaged boilers” can be ambiguous, encompassing scenarios where a burner from one manufacturer is paired with a boiler from another. However, a genuine packaged boiler/burner combination entails a more specific synergy.
Consider a car analogy: For a vehicle to operate seamlessly, its engine and tires must complement each other. Similarly, in a packaged boiler setup, the synergy between the boiler and burner is akin to that between an engine and tires, ensuring optimal performance. With a bona fide packaged boiler, you can have confidence in its ability to maintain a warm and comfortable environment without complications.
Repeatable air/fuel control
Boiler Efficiency Testing is crucial to assess the performance of a boiler system. The efficiency of a boiler hinges on the burner’s ability to maintain the correct air-to-fuel mixture consistently throughout its firing rate, day in and day out, without the need for complex adjustments. While many burner designs claim to achieve this, the reality is that complex linkage designs often fail to maintain air-to-fuel settings over time. Consequently, adjustments are frequently made at high excess air levels to compensate for burner performance inconsistencies, resulting in wasted resources. When selecting a burner, prioritize simplicity in linkage assembly and accessibility for true efficiency and substantial savings over time.
When assessing burner features for Boiler Efficiency Testing, consider fan design. Reverse curve fans offer more reliable air control than squirrel cage fans. Aluminum cast fans with tight tolerances improve efficiency and extend fan life. Opt for a burner with a reverse fan and radial damper design for enhanced combustion air control, efficiency gains, and fuel savings over the boiler’s lifespan.
Heating surface
The heating surface of a boiler, measured in square feet per boiler horsepower, reflects the workload of the vessel. Typically, a firetube boiler adheres to a standard of five square feet per boiler horsepower, a benchmark set by Cleaver-Brooks for its firetube products. This standard is based on rigorous design criteria, ensuring optimal heating surface for extended boiler life and enhanced efficiency.
Vessel design
Designing pressure vessels follows strict rules outlined by the ASME code. However, there are different ways to meet these rules. Key things to think about when designing a pressure vessel include how water moves through it, keeping stress levels low, and making it easy to reach. Look for features like having just one tubesheet, which means fewer welds, better water flow, and less stress on the tubesheet. Also, make sure the tubes are spaced right, the size of the vessel is correct, and the furnace is low. Where you put the inlets and outlets matters too. By including these features, you ensure your boiler works well for a long time. Having accessible front and rear tubesheets makes inspections easier and cuts down on costs for repairs, which saves money in the long run.
Defining Boiler Efficiency
Boiler Efficiency Testing plays a crucial role in assessing the performance of a boiler system across various metrics.
Combustion Efficiency
Boiler Efficiency Testing evaluates a burner’s ability to burn fuel effectively, measured by levels of unburned fuel and excess air in the exhaust. Efficient burners operate with minimal unburned fuel and low excess air levels, typically around 15% for gaseous and liquid fuels. This ensures optimal heat transfer to the load, as less heat is wasted heating excess air. While gaseous and liquid fuels tend to burn more efficiently, solid fuels may exhibit lower combustion efficiency.
Thermal Efficiency
Thermal efficiency measures the heat exchanger’s effectiveness in transferring heat from the combustion process to water or steam. However, it does not consider radiation and convection losses from the boiler’s components. As a result, while thermal efficiency reflects heat exchanger performance, it does not provide a comprehensive assessment of fuel usage and should not be the sole basis for economic evaluations.
Boiler Efficiency
Boiler Efficiency Testing distinguishes “boiler efficiency” from thermal efficiency or fuel-to-steam efficiency. It’s crucial to understand which efficiency metric is being referred to, as thermal efficiency alone does not account for all losses. Fuel-to-steam efficiency, on the other hand, considers radiation and convection losses, providing a more accurate representation of overall boiler efficiency. Before utilizing the term “boiler efficiency” in economic assessments, it’s essential to clarify its definition with the boiler manufacturer to ensure accurate evaluations.
Fuel-To-Steam Efficiency
Fuel-to-steam efficiency serves as a comprehensive measure of a boiler’s overall efficiency, encompassing both heat exchanger performance and losses due to radiation and convection. Boiler Efficiency Testing ensures that fuel-to-steam efficiency is accurately determined, forming the basis for economic evaluations. As outlined in the ASME Power Test Code, PTC 4.1, fuel-to-steam efficiency can be determined through two primary methods: the Input-Output Method and the Heat Loss Method.
Input-Output
Method
The Input-Output method calculates efficiency by comparing the boiler output to its input, expressed in BTUs.
Heat Loss Method
In the Heat Balance method, efficiency is determined by accounting for all heat losses incurred by the boiler. Subtracting the total percent stack, radiation, and convection losses from 100 percent yields the boiler’s fuel-to-steam efficiency. This method comprehensively addresses stack losses, radiation, and convection losses.
Stack Losses
Stack temperature, indicative of the heat carried away by flue gases, plays a crucial role in assessing boiler efficiency. A lower stack temperature signifies more efficient heat exchanger design and higher fuel-to-steam efficiency.
Radiation and Convection Losses
All boilers experience radiation and convection losses, representing heat radiated from the boiler and heat lost due to airflow across it, respectively. While these losses remain relatively constant across boiler types and sizes, they vary with operating pressures.
Components of Efficiency (Impact and Sensitivity)
Understanding efficiency calculations entails recognizing the key factors influencing boiler efficiency. These factors include flue gas temperature (stack temperature), fuel specification, excess air, ambient air temperature, and radiation and convection losses. Flue gas temperature, in particular, requires careful consideration, as manipulating this value can affect the accuracy of efficiency calculations. Ensuring realistic stack temperatures reflective of actual operating conditions is crucial for accurate efficiency assessments.
Fuel Specification
The fuel specification significantly impacts boiler efficiency, especially concerning gaseous fuels where higher hydrogen content leads to increased water vapor formation during combustion. This water vapor consumes energy during phase changes, resulting in lower efficiency. For instance, fuel oil tends to exhibit higher efficiency levels compared to natural gas due to these water vapor losses. It’s imperative to use a fuel specification representative of the actual fuel used at the job site for accurate efficiency calculations. Evaluating efficiency guarantees or calculations should involve verifying the representativeness of the fuel specification, as using fuel with low hydrogen content can yield inaccurate assessments of fuel usage efficiency.
Excess Air
To maintain safety and efficiency, it’s important to control excess air in burners. Excess air helps prevent fuel-rich conditions but can reduce energy transfer to water. A good burner design aims for 15% excess air with 3% oxygen in flue gas. Despite seasonal variations, sticking to 15% excess air ensures safety. Ensure burners have reliable damper and linkage features for accurate efficiency calculations and fuel assessments.
Ambient Temperature
Ambient temperature significantly impacts boiler efficiency. A mere 40-degree change can alter efficiency by 1% or more. Boiler rooms are usually warm, with efficiency calculations often using an 80°F ambient temperature. When evaluating efficiency, ensure correct ambient air conditions are considered. Using a value above 80°F goes against standard practice. For outdoor boilers, lower ambient temperatures reduce efficiency regardless of design. Request efficiency calculations based on lower temperatures for accurate fuel use assessment.
Radiation and Convection Losses
Radiation and convection losses occur when heat escapes from the boiler vessel, despite insulation efforts. Inaccurate fuel estimates can result from efficiency ratings that overlook these losses. Boiler design impacts these losses; for instance, waterback boilers have higher rear skin temperatures than dryback designs. Touching the rear door of a dryback boiler can reveal the difference – cooler temperatures signify lower losses. Boilers with high rear temperatures waste energy. Airflow across the boiler, usually low indoors, also affects losses. Outdoor boilers face increased radiation and convection losses.
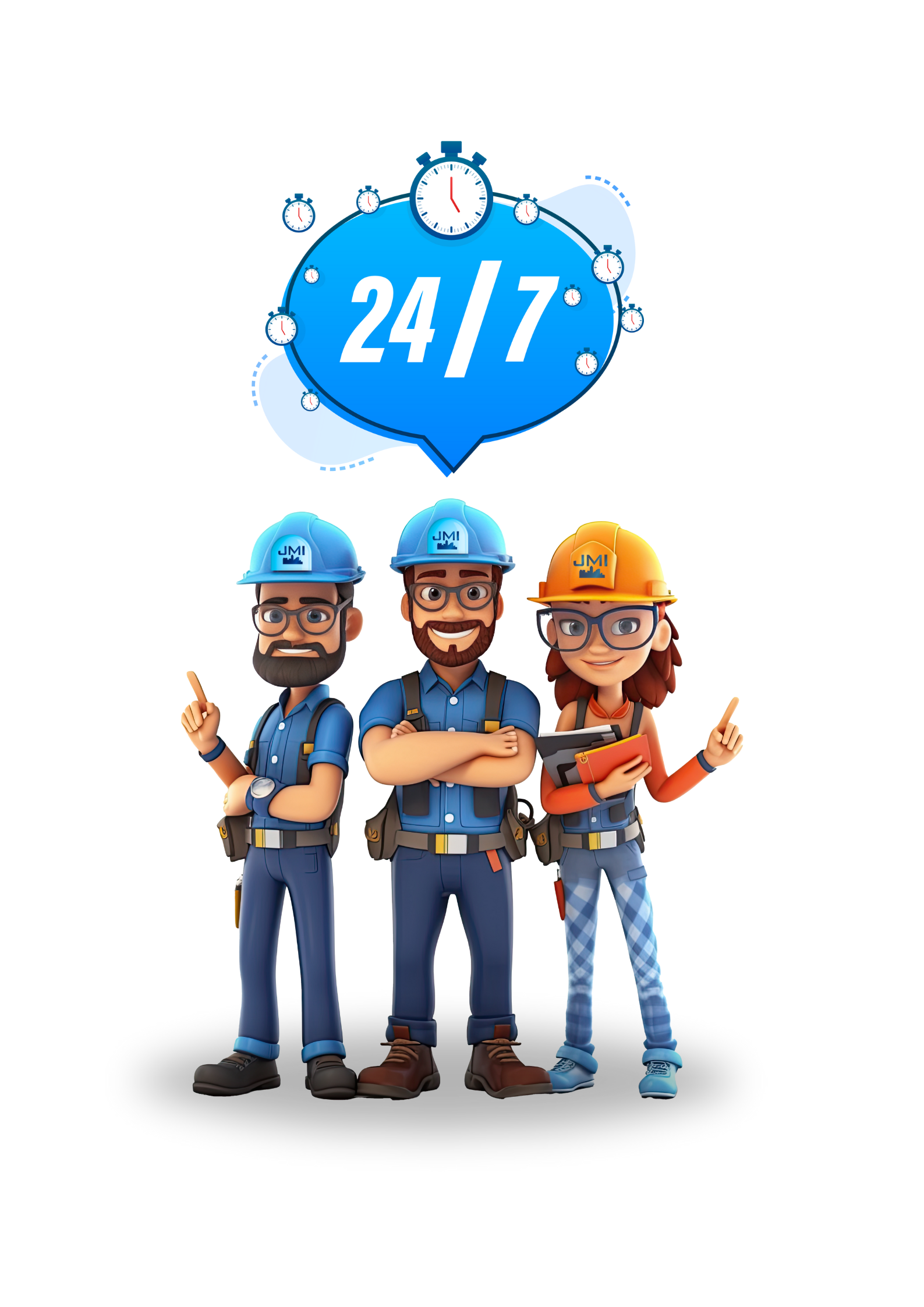
Reach Out To Us!
When evaluating your boiler purchase, ensure your boiler vendor provides a thorough efficiency calculation substantiated by realistic and proven data. Additionally, review the type of boiler/burner utilized to ascertain consistent and repeatable performance. Ultimately, you’ll pay for the actual fuel consumed, not an estimate based on efficiency calculations. Optimal high-efficiency boiler designs deliver superior performance, with efficiency calculations capable of verification and substantiation. Prioritize understanding the actual fuel usage requirements before making a purchase decision. Investing time in evaluating efficiency will yield dividends, particularly when opting for a high-efficiency, repeatable design firetube boiler, ensuring sustained benefits throughout its operational lifespan.
Do you have any questions or need advice? Feel free to reach out to us by giving us a call at 317-243-7180. We’re here to help and offer customized guidance based on your specific needs.
FREE QUOTE
Do you need help with HVAC or Plumbing service or maintenance? Fill out this form to get in touch with JMI Mechanical.
OFFICE LINE
ADDRESS
5610 Dividend Rd. Suite A, Indianapolis, IN 46241
WORKING HOURS
OPEN 24/7/365
OFFICE LINE
ADDRESS
5610 Dividend Rd Suite A, Indianapolis, IN 46241
WORKING HOURS